Title: Design of Welding Fixture
Client: ICEM
Software used: Ansys Mechanical
Duration: 1 Months
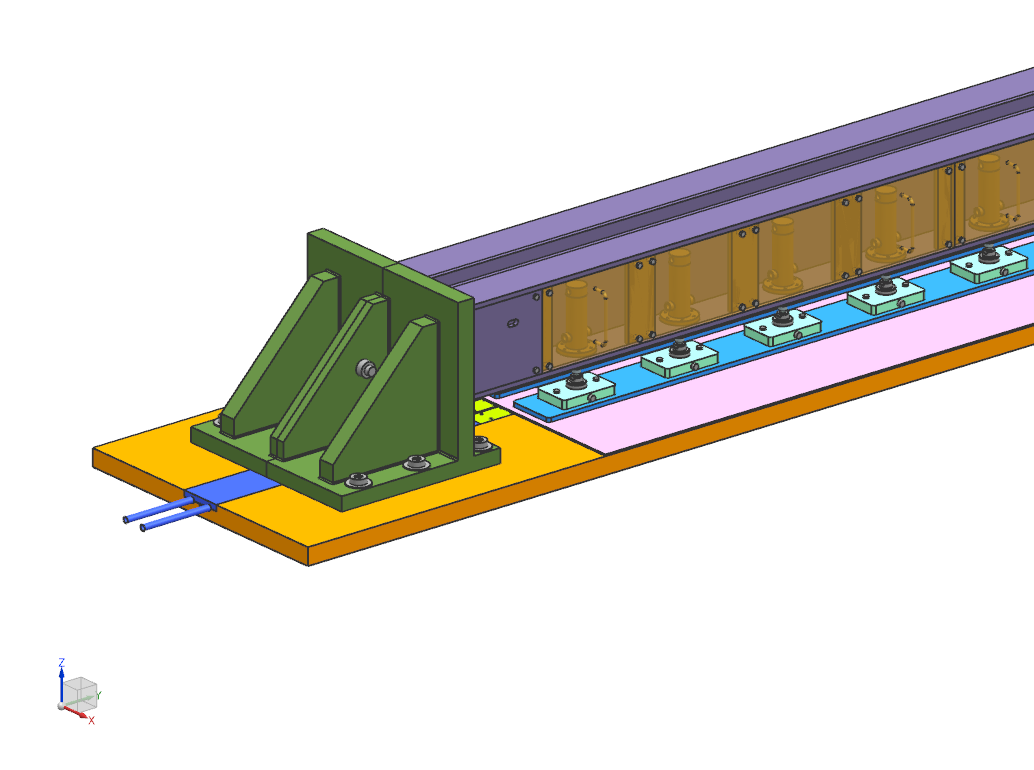
Keywords: Welding, distortion, stainless steel, fixture, copper, cooling, clamping
Welding is one of the most commonly used processes in manufacturing industry. There are numerous types of welding processes based on the material to be welded, the geometry of the welded components, the type of finishing required, the strength required for the weld and many more. However, there are many challenges to provide a weld without having adverse effect on the welded components. Distortion of the plates during welding often happens for smaller thickness plates. The problem of distortion of stainless-steel plates is addressed in this project. The root cause of the distortion is identified. During welding process, high heat flux is added in a localised area, which causes high temperature gradient. To avoid distortion, a fixture is designed to implement two parallel approaches. One, to cool down the high temperature at the heat affected zone as early as possible after the welding in a particular area is completed. This is achieved by placing copper plates below the welded area and passing water through the plates for cooling. Two, to hold the plates by a clamping force, so that even after the high temperature gradient, the distortion will be prevented. In addition to the avoiding the distortion challenge, an efficient handling of the plates is also achieved by roller supports and hydraulic arrangements. Successful welding of plates ranging from 5 mm to 10 mm with a length of 6 m to 7 m is done with minimum distortion.
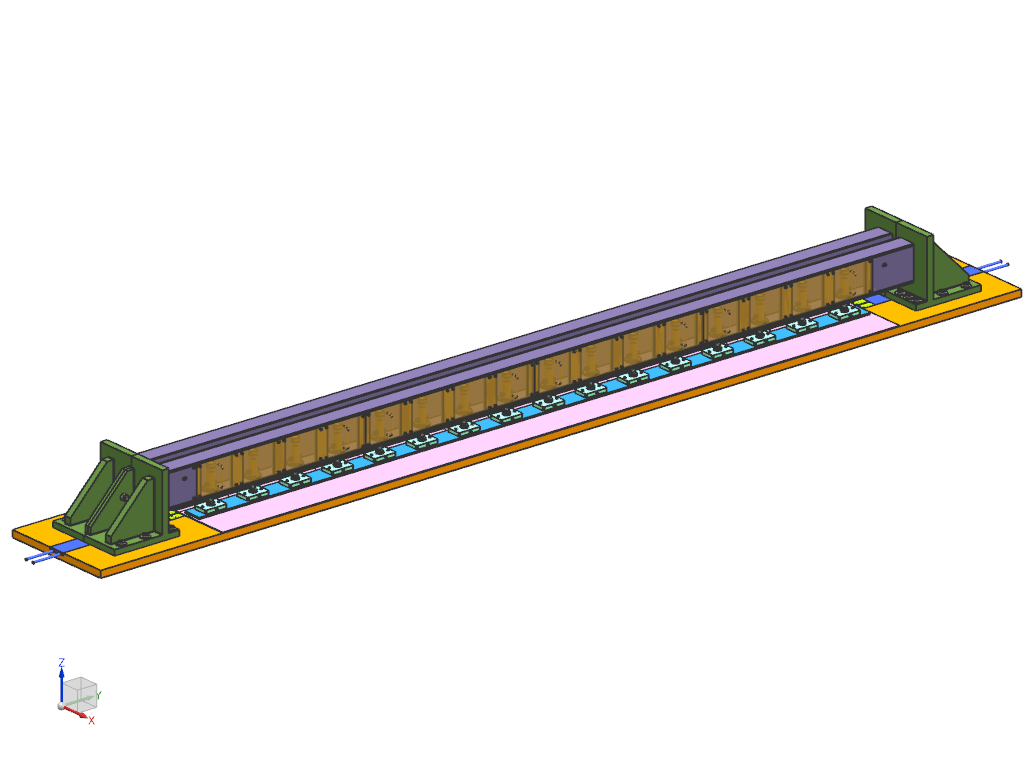
Benchmark: Plate distortion during welding is one of the critical problems to be addressed in the manufacturing industry. The distortion of long and relatively thin SS plates during welding was successfully controlled by the fixture designed with a combination of clamping and cooling arrangement.
Recent Projects